1. МОНТАЖ ЧУГУННЫХ ТРУБОПРОВОДОВ
Доставленные на трассу строительства трубы подвергают приемке и проверке качества. Каждую трубу осматривают для обнаружения трещин, раковин, наростов и других дефектов. Трубы с такими дефектами, также издающие дребезжащий звук (из-за трещин, скрытых под изоляцией), к укладке не допускаются. При приемке труб проверяют наружный диаметр цилиндрической их части и внутренние диаметры раструбов. Источник статьи: www.sbh.ru
Трубы вдоль траншеи раскладывают на расстоянии не менее 1- 1,5 м от бровки траншеи (рис. 20.1, а), располагая их в таком направлении, в каком они должны быть уложены в траншее (т.е. против движения жидкости по будущему трубопроводу).
В начале монтируемого участка трубопровода, особенно при заделке раструбных стыков самоуплотняющимися резиновыми манжетами, устраивают концевой бетонный упор для первых труб.- Легкие трубы (диаметром до 200 мм) опускают в траншею вручную. с помощью каната, который пропускают внутри трубы или которым обвязывают трубу у концов. Трубы диаметром более 200 мм укладывают обычно с помощью монтажных стреловых кранов или кранов-трубоукладчиков. Причем трубы в траншею укладывают стреловыми (автомобильными, пневмоколесными, гусеничными) кранами при такой их раскладке на берме, когда в процессе монтажа требуется после строповки трубы ее подъем и поворот (см. рис. 20.1, а), а кранами-трубоукладчиками - в том случае, когда трубы разложены таким образом (см. рис. 20.2), когда не требуется поворот крана.
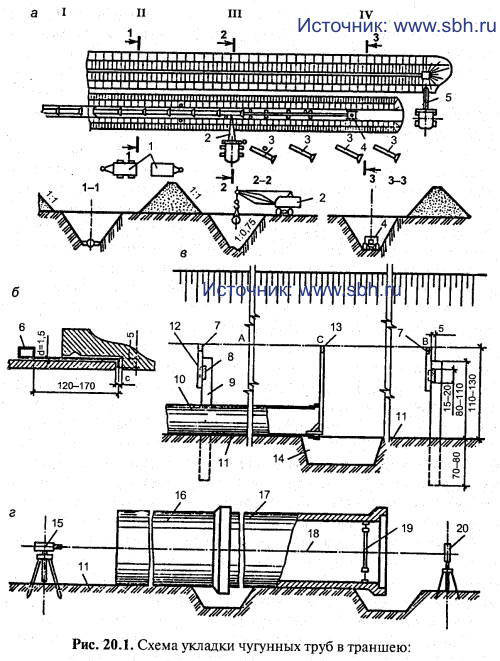
Рис. 20.1. Схема укладки чугунных труб в траншею:
I — предварительное гидравлическое испытание ; II — присыпка грунтом до 0.5 диаметра с уплотнением ; III — укладка труб и монтаж ; IV — устройство профилированного основания ; 1 — передвижные временные здания ; 2 - — гусеничный кран ; 3 — трубы ( раскладка ); 4 — бульдозер ; 5 — экскаватор ; б — проволочный крюк - шаблон ; 7 — постоянная визирка ; 8, 9 —доска и столбы обноски ; 10 — труба ; 1 1 — дно Траншеи : 12 — полочка ; 13 — ходовая визирка ; 14 — приямок для стыкования труб ; 15 — лазерный нивелир ; 76 — уложенная труба ; 17 — укладываемая труба ; 18 — ось трубопровода ( луч лазерного нивелира ); 19 — полупрозрачный экран для центрирования луча ; 20 — экран |
Статья подготовлена и представлена в цифровом виде
компанией "SBH COTPAHC"
Опущенную в траншею трубу заводят гладким концом в раструб ранее уложенной. При этом следят, чтобы он не доходил до упора раструба на расстояние, равное в зависимости от диаметра труб от 5 до 9 мм при заделке стыка прядью и от 5 до 10 мм при заделке резиновой манжетой. Для проверки наличия такого зазора применяют проволочный крюк-шаблон (рис. 20. 1, 6), который после ввода в раструб поворачивают на 90°.
После заводки гладкого конца чугунной трубы в раструб ранее уложенной производят ее центрирование, затем приступают к центрированию раструбного конца укладываемой трубы по оси трубопровода в горизонтальном и вертикальном направлениях. В горизонтальном направлении трубы центрируют с помошью отвеса, подвешенного к тонкой проволоке, которую натягивают между обносками по оси трубопровода. Центрирование в вертикальном направлении часто необходимо для укладки труб по заданному уклону и поэтому положение раструбного конца укладываемой трубы проверяют или путем визирования, или с применением лазерного нивелира. При способе визирования в начале и конце укладываемого участка трубопровода устанавливают обноски (рис. 20.1, в), к которым прикрепляют постоянные визирки, верхние кромки которых А и В находятся на одинаковой высоте от трубы с учетом заданного уклона. Высота этих визирок должна быть примерно на уровне глаз. Таким образом, визирная ось АВ будет параллельна проектной оси трубопровода. Для проверки правильности укладки труб делают ходовую визирку длиной, равной расстоянию от лотка трубы до оси АВ. В процессе укладки каждой трубы на ее лоток устанавливают ходовую визирку (рис. 20.1, в). Взглядом с одной неподвижной визирки А на другую В проверяют положение ходовой визирки в точке С. Постоянные визирки в траншеях с откосами устанавливают непосредственно в траншее, а при укладке труб в траншеи с вертикальными откосами и креплениями — над траншеей.
При укладке труб по заданному уклону с помощью лазерного нивелира (рис. 20.1, г) его устанавливают в начале участка и налаживают так, чтобы его луч в точности совпадал с продольной осью трубопровода.
Схема организации работ при укладке труб кран ом-трубоукладчиком приведена на рис. 20.2. 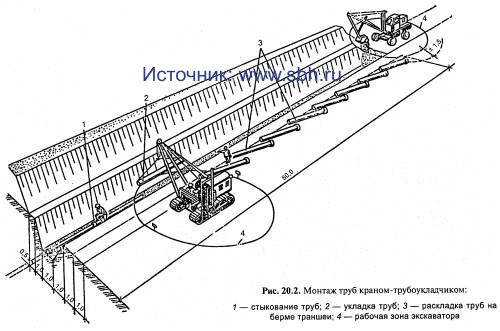
Герметичность и водонепроницаемость раструбных стыков чугунных трубопроводов достигается заделкой раструбной щели пеньковой просмоленной и битуминизированной прядью с последующим устройством замка из асбестоцементной смеси, удерживающего прядь от выдавливания гидравлическим давлением. В последнее времяприменяют мастики-герметики. При заделке стыков самоуплотняющимися резиновыми манжетами устройство замков не требуется.
Заделка раструбных стыков прядью. Пеньковую прядь вводят в раструбную щель до упора раструба на такую глубину, чтобы осталось место для устройства замка. Поскольку толщина жгута из пряди несколько превышает ширину раструбной щели, его проталкивают в стык с помощью конопатки. Сначала от руки, а затем сильными ударами молотка (при ручной чеканке) жгут вводят в кольцевой зазор. При механической чеканке жгут уплотняют пневматическим инструментом. Для создания требуемой герметичности стыка обычно закладывают в щель два-три жгута, причем так, чтобы захлесты их не совпадали по длине окружности. После заделки стыка прядью делают асбестоцементный замок. Источник статьи: www.sbh.ru
Монтаж и устройство стыков на резиновых манжетах. При монтаже чугунных труб со стыковыми соединениями на резиновых манжетах стык уплотняется благодаря радиальному сжатию манжеты в раструбной щели. Трубы на стыках с самоуплотняющимися резиновыми манжетами монтируют следующим образом. Трубу краном подают в траншею по направлению укладки трубопровода на расстоянии 0,4 - 0,5 м от раструба уложенной трубы, удерживая ее на весу. Далее с помощью шаблона и мела размечают линии ограничения ввода гладкого конца в раструб с учетом необходимого зазора (рис. 20.3, а), после чего в паз раструба закладывают резиновую манжету (рис. 20.3, б). Одновременно наружную поверхность гладкого конца трубы до линии ограничения и внутреннюю поверхность манжеты смазывают графитно- глицериновой смазкой (рис. 20.3, в), а затем монтируемую трубу центрируют и с помощью монтажного приспособления вводят в раструб ранее уложенной до ограничительной линии (рис. 20.3, г). Поскольку при монтаже стыков чугунных труб на резиновых манжетах требуются большие усилия, применяют различные приспособления и устройства, приведенные на рис. 20.3, д—л. После ввода втулочного конца трубы в раструб ранее уложенной центрируют раструбный конец укладываемой трубы и закрепляют положение ее подсыпкой грунта в пазухи с уплотнением до половины диаметра, оставляя не засыпанными приямки и стыковые соединения.
Основная задача при монтаже чугунных труб на резиновых манжетах - создание осевого усилия, необходимого для соединения труб. На практике получили распространение несколько типов приспособлений для стыковки труб (см. рис. 20.3). Основой простейшего из них является домкрат, расположенный между захватами укладываемой и ранее уложенной трубы.
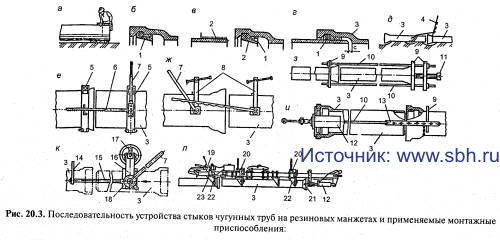
Рис. 20.3. Последовательность устройства стыков чугунных труб на резиновых манжетах и применяемые монтажные приспособления:
а - разметка линии ограничения ввода гладкого конца в раструб; б - закладка резиновой манжеты; в - смазка гладкого конца трубы; г - смонтированный готовый стык; д - рычажно-троссовое приспособление; е - реечное приспособление с зубчатой рейкой и двумя хомутами-захватами; ж - то же, с двумя винтовыми захватами; з - монтажное приспособление с центральным торцевым винтом; и - приспособление с гибкими тягами и гидроцилиндров; к - приспособление треста "Востокгидроспецстрой"; л - то же треста "Укрводстрой"; 1 - резиновая манжета; 2 - смазка; 3 - монтажная труба; 4 - рычажно-троссовое приспособление; 5 - хомуты; 6 - зубчатая рейка; 7 - рычаг; 8 - винтовые захваты; 9 - упоры; 10 - тяга; 11 - винт с ручкой; 12 - гидроцилиндр; 13 - регулировочные планки; 14 - скоба; 15 - трос; 16 - корпус приспособления; 17 - винт со штурвалом; 18 - колодки; 19 - гидрораспределитель; 20 - грузозахватные устройства; 21 - быстроразъёмные захваты; 22 - упорное седло; 23 - гидронасос |
Однако в последние годы в целях ускорения и облегчения процесса монтажа чугунных труб на резиновых уплотнителях на практике созданы и применяются ряд новых более эффективных приспособлений в виде навесного оборудования. На рис. 20. 4, а представлено такое устройство для монтажа чугунных раструбных труб диаметром от 100 до 250 мм с резиновыми уплотнительными манжетами.
Применение указанного устройства позволяет повысить производительность труда и снизить трудоемкость монтажа трубопроводов.
Привод стыковочных устройств осуществляют от базовой машины, однако при производстве работ необходимо постоянное нахождение рабочих в траншее. Монтажные операции с бермы, т.е. без присутствия рабочих в траншее, выполняют навесным оборудованием, разработанным Тульским политехническим институтом и трестом Туласпецстрой (рис. 20.4, 6).
Монтаж чугунных труб диаметром 300 мм на резиновых уплотни- тельных кольцах производят различными средствами, а зачеканку чугунных труб диаметром свыше 300 мм прядью - вручную.
В целях облегчения этого процесса разработано навесное оборудование для монтажа и зачеканки стыковых соединений чугунных труб волокнистыми материалами (рис. 20.4, в). Основным узлом этого навесного оборудования является стыковочный манипулятор.
Устройство с трубой опускают в траншею на место укладки так, чтобы торец щеки подвижного захвата уперся в торец раструба ранее уложенной трубы. Описанное устройство может быть использовано и на монтаже труб на резиновых уплотнительных кольцах.
В Главомскпромстрое разработан манипулятор для подачи, укладки и стыковки чугунных труб. Он применяется как навесное оборудование к экскаватору ЭО-3322А. Конструкция манипулятора представляет собой траверсу с двумя захватами.
Мастиками-герметиками заделывают стыковые соединения раструбных чугунных труб при прокладке напорных канализационных трубопроводов с максимальным рабочим давлением до 0,5 МПа. При этом чаще всего применяют полисульфидные герметики из герметизирующих и вулканизирующих паст с добавлением иногда асбестовой или резиновой крошки. Приготовляют мастики-герметики на месте работ за 30—60 мин до их использования. Стыки герметизируют с помощью шприцев с ручным или пневматическим выдавливанием мастики или с помощью пневматических установок.
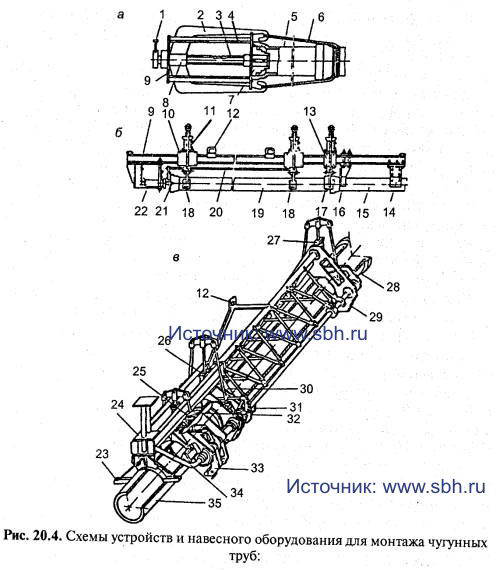
Рис. 20.4. Схемы устройств и навесного оборудования для монтажа чугунныхтруб:
а — простейшее устройство для монтажа труб ; б — навесное оборудование конструкции Тульского политехнического института и треста Туласпецстрой ; в — навесное оборудование для монтажа и зачеканки чугунных труб ; 1 — вороток - 2 — рычаги ; 3 — винт ; 4 — стойки ; 5, 19 — монтируемые трубы ; 6 — гибкие тяги ' 7 - упорно - направляющий диск ; 8 - гайка ; 9 - траверсы ; 10 - каретки подвижные ; 11 - гидроцилиндры ; « - скоба ; 13 — каретка неподвижная ; 14- хомут - 15, 35 — ранее уложенная труба ; 16 — упор ; 17 — захват конусный - « — захваты подвижные ; 20 - тяга ; 21 - диск нажимной ; 22 - гидродомкрат нажимной - 23 — вилка опорная ; 24 — рама ; 25 — прядь пеньковая ; 26 — гидроцилиндры подвижного и неподвижного захватов ; 27 — гидроцилиндр правого хвата ' 28 — труба укладываемая ; 29 — захват неподвижный ; 30 — упор правый ; 31 ~ гидроцилиндр перемещения чеканов ; 32 — чеканы ; 33 — схват подвижного захвата ; 34 — гидроцилиндр подачи трубы
|
Статья подготовлена и представлена в цифровом виде
компанией "SBH COTPAHC"
2. УКРУПНИТЕЛЬНАЯ СБОРКА, СВАРКА И ИЗОЛЯЦИЯ СТАЛЬНЫХ ТРУБ НА ТРУБОЗАГОТОВИТЕЛЬНЫХ БАЗАХ
В целях индустриализации строительства трубопроводов и ускорения темпов производства работ в последние годы широко применяют метол предварительной укрупнительной сборки и сварки труб в секции (звенья) и их изоляции на трубосварочных и трубоизоляци-онных базах, после чего их транспортируют на трассу для укладки в траншею. Базы снабжены современным оборудованием для полуавтоматической и автоматической сварки поворотных стыков, а также устройствами для очистки и последующего нанесения на трубные секции противокоррозионных покрытий.
Базы практически состоят из трех основных технологических линий - сборки (центровки), сварки и изоляции (рис. 20.5, а). Они бывают стационарные, полустационарные и полевые.
Переработка труб на стационарных базах организуется следующим образом. Трубы краном укладывают на приемных стеллажах, откуда подают на линию сборки (центровки), где с помощью центратора собирают в секции длиной 18, 24 и 36 м. После сборки на каждом стыке вначале выполняют «прихватку», а затем полуавтоматическую сварку первого (корневого) слоя шва. Затем секцию через промежуточный стеллаж-накопитель подают на линию автоматической сварки последующих слоев. Сваренную секцию подают на линию изоляции, где производят операции сушки, грунтовки (праймирования) и изоляции. Готовую изолированную секцию перемещают под кран-перегружатель, который подает ее на склад готовой продукции или на трубоплетевоз.
На стационарных и полустаииопарных базах сварку труб чаще всего выполняют под флюсом трубосварочными головками типа ПТ-56, а первый (корневой) шов сваривают полуавтоматически в среде углекислого газа плавящимся электродом (цельной сварочной проволокой) или без дополнительной защиты порошковой проволокой с помощью полуавтомата А-547 р. Для сборки и сварки труб в секции длиной 36—40 м в полевых условиях используют полевые трубосварочные базы (рис. 20.5, б). Такие базы располагают вдоль трассы строящегося трубопровода обычно через 15—30 км друг от друга. При их развертывании используют оборудование типовой базы БАС-1. Источник статьи: www.sbh.ru
Изготовление криволинейных элементов. Сварные отводы изготовляют из отдельных секторов. Отвод с углом 90° состоит из четырех секторов: двух внутренних с углом 30" каждый и двух наружных с углом 15° каждый. Отвод с углом 60° можно выполнять из двух секторов с углом 30° каждый. Отводы больших диаметров (600 мм и выше) можно изготовить как из листового металла, так и из труб.
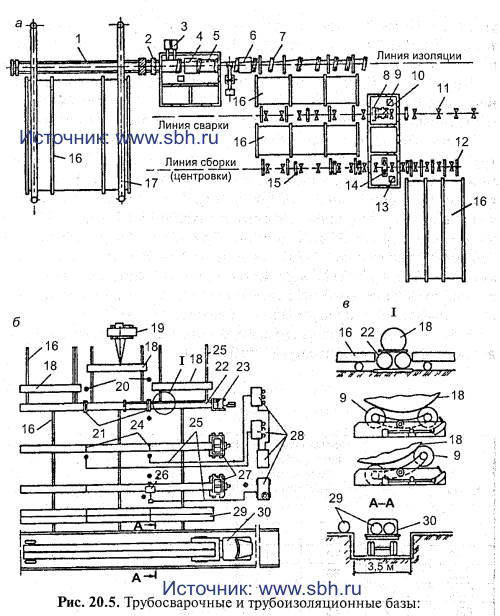
Рис. 20.5. Трубосварочные и трубоизоляштонные базы:
а — стационарная база ; б — полевая база типа БАС -1 ; в — роликовые опоры при сварке труб и подаче сваренной трубной секции ; 1 — роликовый путь ; 2, 3 — приводная и промежуточная тележки ; 4 — битумоллавильный котел ; 5 — изоляционная ванна ; 6 — установка сушки грунтовки ; 7 — нанесение грунтовки ; 8 — установка сушки секций перед очисткой ; 9 — роликовые опоры ; 10 — зачистные щетки ; 11 — стеллаж - накопитель ; 12 — вращатель ; 73 — пульт управления ; 14 — установка автоматической сварки труб ; 15 — ролик продольного перемещения трубы ; 16 — стеллажи ; 17 — кран - перегружатель ; 18 — - трубы ; 19 — кран - трубоукладчик ; 20 — сварщики , монтажники и машинисты ; 21 — центратор ; 22 — сварочный стенд ; 23 — лебедка ; 24 — корневые швы ; 25 — кабель ; 26 — окончательная сварка стыка ; 27 — торцовые вращатели ; 28 — сварочные установки СЧУ -2; 29 — готовые секции труб ; 30 — трубоплетевоз |
При ручной резке труб на секторы применяют приспособления или шаблоны, а при изготовлении секторов из листоного металла заготовки размечают по шаблонам, а затем вырезают и вальцуют.
Гнутье труб необходимо в тех случаях, когда естественный изгиб трубопроводов в вертикальной и горизонтальных плоскостях невозможен. Тогда кривые необходимого радиуса и угла получают путем вварки предварительно изогнутых колен, изготовленных способом холодного гнутья на трубогибочных станках типа ГТ для труб больших диаметров с применением дорнов. Причем трубы диаметром 273— 530 мм гнут на станке ГТ-531, диаметром 720-1020 мм - ГТ-102!, диаметром 1220 - ГТ-2121 и диаметром 1420 - на станке ГТ-1421. Для гнутья подбирают трубы с более толстыми стенками и с отклонениями от диаметра в сторону положительного допуска.
Минимально допустимые радиусы кривых при гнутье труб в ходлодном состоянии приведены в табл. 20.1.
Таблица 20.1 Минимально допустимые радиусы кривых вставок
Диаметр трубы, мм |
Толщина стенки , мм |
Наименьший радиус изгиба трубы, м, при толщине стенки |
Диаметр трубы, мм |
Толщина стенки , мм |
Наименьший радиус изгиба трубы, м, при толщине стенки |
Минимальный |
Максимальный |
Минимальный |
Максимальный |
1420 |
12-20 |
70 |
40 |
630 |
6-11 |
25 |
15 |
1220 |
10-18 |
60 |
30 |
530 |
6-9 |
15 |
10 |
1020 |
9-16 |
50 |
25 |
426 |
6-9 |
10 |
8 |
820 |
8-12 |
35 |
25 |
300-400 |
4-8 |
8 |
5 |
720 |
7-12 |
30 |
20 |
200-300 |
4-7 |
5 |
3 |
Примечание: Допускается уменьшение величины наименьшего радиуса изгиба на 10%.
3. СБОРКА, СВАРКА И ИЗОЛЯЦИЯ ТРУБ И ТРУБНЫХ СЕКЦИЙ
Стальные трубы соединяют между собой на сварке, а в местах установки арматуры (задвижек, кранов, вентилей и др.) — на фланцах.
Сварка труб включает следующие технологические операции: подготовка труб и кромок их торцов к сборке; раскладка труб на сварочных подкладках (стеллажах или стендах); центровка и стягивание труб до достижения между кромками торцов нужного зазора; скрепление собранного стыка сварочными прихватами; сварка стыка. При подготовке труб очищают кромки шириной 10—15 мм соединяемых труб от грязи, ржавчины и особенно от масел, выравнивают вмятины и неровности торцов, выправляют овальность, чтобы разность диаметров торцов не превышала 1 — 1,25 % номинала. Толщина стенок соединяемых труб не должна иметь отклонения более 12—15 % стандартного размера.
Раскладка труб перед сборкой должна способствовать их беспрепятственной и удобной центровке — совмещению геометрических осей и кромок, труб при строгом соблюдении нормативных зазоров. Для этого применяют специальные зажимы - центраторы, которые бывают наружные (винтовые, эксцентриковые и цепные, рис. 20.6, а—в) и внутренние (гидравлические, рис. 20.6, г). Благодаря синхронному действию разжимных кулачков центраторы автоматически обеспечивают калибровку и центровку торцов труб.Дуговую сварку стальных труб (рис. 20.6, д) осуществляют с поворотом их вокруг своей оси (поворотные стыки) и без поворота (неповоротные или потолочные стыки). Неповоротные стыки сваривают в два или три слоя, начиная с нижней образующей трубы в 50 мм от вертикального диаметра труб (рис. 20.6, е). Первый слой, как уже указывалось, называют корневым, второй — заполняющим и последний - облицовочным. Трубы диаметром до 500 мм сваривают непрерывным швом, а трубы больших диаметров — прерывистым (как показано стрелками на рис. 20.6, е). Неповоротные стыки труб больших диаметров при необходимости ускорения производства работ сваривают одновременно два или три сварщика по схемам, приведенным на рис. 20.6, и, к, п.
Качество сварных соединений труб в значительной степени зависит от режима сварки, который определяют параметры и характер тока, его полярность, длина дуги, скорость сварки, амплитуда колебаний и вылег электродов, их размер и состав покрытия, температура основного материала труб в момент начала сварки. Так, увеличение силы тока и обратная полярность способствуют улучшению проплавления металла и увеличению глубины провара, а с увеличением силы тока повышается скорость сварки и т.д.
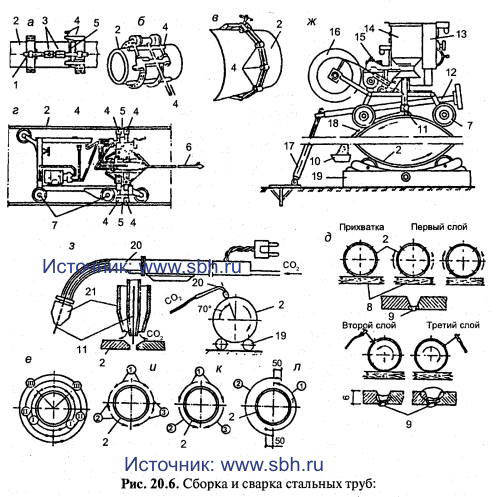
Рис. 20.6. Сборка и сварка стальных труб:
а , б — центраторы винтовой и эксцентриковые ( для труб диаметром не более 350 мм ); в —тоже , наружный роликово - звеньевой ( для труб 520-1020 мм ); г — то же , внутренний гидравлический ( для труб 520-1220 мм ); д , е — последовательность операций при ручной электросварке стыков поворотным и неповоротным трехслойным швом ; ж— схема применения сварочной головки ПТ -56 для поворотной сварки стыков под слоем флюса ; э — то же , для сварки корня шва шланговым держателем полуавтомата А -547- р ; и , е — порядок наложения корневого слоя шва при сварке труб большого диаметра тремя сварщиками ; л — то же , для заполнения остальной части шва двумя сварщиками ; 1 — натяжной винт ; 2 — свариваемые трубы ; 3 — отверстие для воронки ; 4 — центрирующие элементы ; 5 — стык трубы ; 6 — штанга ; 7 — ролики ; 8 — лежни под трубы ; 9 — корневой спой шва ; 10 — сборник для флюсов ; 11— проволока для сварки ; 12 — регулировочный винт ; 13 - панель с реостатом , вольтметром и выключателями ; 14 — бункер для флюса ; 15 — подающий механизм с двигателем и редуктором ; 16 — кассета со сварочной проволокой ; 17 — штатив ; 18— флюс ; 19 — штанговый держатель ; 20 — головка держателя ; 1, 2, 3 в кружках — позиции сварщиков ; I, II, III — последовательность наложения шва неповоротного стыка |
Однако, поскольку ручная сварка неповоротных стыков очень трудоемка и часто сдерживает темп прокладки трубопровода, в последнее время все чаще применяют прогрессивную полуавтоматическую и автоматическую сварку таких стыков с помощью, например, сварочного автомата, состоящего из самоходной тележки, сварочной головки и пульта управления. В процессе сварки головка перемещается вокруг трубы по направляющему поясу и сваривает трубы электродной проволокой.
Для сварки труб диаметром 1420 мм с толщиной стенки 20 мм применяют комплекс оборудования "Дуга-2", включающий станок для обработки кромок, центратор-автомат для сборки труб и варки внутри первого (корневого) слоя шва, сварочные головки-автоматы для сварки наружных слоев, а также агрегат питания. Им можно сваривать до 38 стыков в смену при скорости сварки до 70 м/ч.
Особо эффективным в полевых условиях оказался новый способ электроконтактной стыковой сварки путем непрерывного оплавле- ния торцов труб с помощью установки типа ТКУС (для сварки труб в секции) и типа ТКУП (для сварки секций в нитку трубопровода). Трубы диаметром 1420 мм сваривают установкой типа ТКУП, названной «Север- 1». В ее состав входят сварочная машина К-700 с внутренним гратоснимателем, передвижная дизельная электростанция, агрегаты для зачистки концов труб и снятия наружного грата. Все агрегаты установки оснащены системами автоматического управления процессом сварки. Им можно сваривать до 50-60 стыков труб такого диаметра в смену.
На сварочных базах (стационарных и полустационарных) сварку труб в секции чаще всего выполняют под флюсом с помощью сварочной головки, например, типа ПТ-56 (рис. 20.6, ж), корневой шов - под защитой углекислого газа с помощью полуавтомата А-547р (рис. 20.6, з). Для сборки и сварки труб в секции длиной до 40 м в полевых условиях оборудуют трубосварочные базы (ТСБ) вблизи трассы с плечом обслуживания 25—30 км.
Трубопроводы из стальных труб предназначены для длительной эксплуатации. Однако если их уложить в грунт без надежной изоляции, они сравнительно быстро разрушаются от воздействия почвенной коррозии и блуждающих электрических токов (электрокоррозия). Поэтому чтобы удлинить срок службы трубопроводов и обеспечить их безаварийную работу, необходимо их защитить от обоих видов коррозии.
Виды изоляционных покрытий. Покрытия должны обладать плотностью, обеспечивающей гидро- и электроизоляционные свойства, хорошей прилипаемостью к металлу (адгезией), устойчивостью к температурным изменениям и способностью сохранять свою форму в условиях окружающей среды (пластичностью), выдерживать значительные нагрузки в процессе укладки (механической прочностью).
Наиболее эффективной для обеспечения долговечности трубопровода является комплексная противокоррозионная его защита, включающая так называемую «пассивную» их защиту различными изоляционными покрытиями и "активную» (катодную, протекторную и дренажную) защиту от воздействия блуждающих токов (электрокоррозии), ибо она часто бывает опаснее почвенной (гальванокоррозии).
Принцип действия катодной, протекторной и электродренажной защиты стальных труб от электрокоррозии заключается в следующем. Вблизи трубопровода оборудуют станцию катодной защиты (СКЗ), в состав которой входят источник постоянного тока, анодное заземление и дренажные кабели. Отрицательную клемму источника тока присоединяют к стальному трубопроводу, а положительную — к заземлению. В результате ток стекает с анодного заземления, подтекает к трубопроводу и возвращается к источнику по дренажному кабелю. Ток СКЗ создает отрицательный потенциал на трубопроводе и при его работе происходит разрушение анодного заземления, но при этом одновременно защищается стальной подземный трубопровод.
Протекторную защиту применяют для защиты стальных трубопроводов небольшой протяженности от коррозии блуждающими токами, если необходимое смещение потенциала трубопровода не превышает 0,3 В. Протектор изготавливают из металла с более отрицательным электродным потенциалом, чем металл подземного трубопровода. Установленный в грунт и приведенный в контакт с трубопроводом протектор вместе с ним образует гальваническую пару. Протектор (гальванический анод) при этом разрушается, а подземный трубопровод поляризуется до защитных потенциалов и не разрушается.
Электродренажная защита стальных трубопроводов заключается в отводе блуждающих токов, проникших в трубопровод, в сеть обратных токов электрического рельсового транспорта путем присоединения трубопровода через дренажное устройство с элементами этой сети (отрицательной шиной тяговой подстанции, отсасывающим пунктом или рельсом). Благодаря этому на трубопроводе создается отрицательный потенциал, что предотвращает выход блуждающих токов из металла трубы в почву и ее разрушение.
Для защиты трубопроводов от почвенной коррозии применяют главным образом покрытия на основе нефтяных битумов, а также из полимерных липких лент.
Конструктивно изоляционные покрытия состоят из грунтовки, одного или нескольких слоев изоляционного материала (мастики, липкой ленты), армирующего и оберточного слоев. Они бывают трех основных типов: нормальные, усиленные и весьма усиленные. Для магистральных трубопроводов применяют покрытия нормального и усиленного типов, а для разводящих, проложенных в пределах города или промышленного предприятия, весьма усиленного типа.
Покрытие весьма усиленного типа общей толщиной 9±0,5 мм состоит из одного слоя битумной грунтовки, трех слоев мастики толщиной по 3 мм, разделяемых двумя слоями армирующей обмотки из стеклохолста, и наружной обертки из прочной крафт-бумаги. Источник статьи: www.sbh.ru
Нормальное покрытие состоит из грунтовки, мастики слоем 4 мм, одного слоя стеклохолста и защитной обертки.
Усиленное покрытие, нанесенное в базовых условиях, состоит из грунтовки, двух слоев мастики по 3 мм, двух слоев стеклохолста и защитной обертки, а в полевых условиях — из грунтовки, одного слоя мастики 6 мм, одного слоя стеклохолста и защитной обертки.
Покрытия из полимерных липких лент удачно сочетают в себе высокую защитную способность и технологичность при механизированном их нанесении. Такие ленты изготавливают из полиэтилена или поливинилхлорида с нанесением на них клеевого слоя. Покрытия состоят из слоя грунтовки, одного, двух или трех слоев ленты (что соответствует нормальной, усиленной и весьма усиленной изоляции) и защитной обертки.
Нанесение изоляционных покрытий. Перед нанесением покрытий поверхность трубопровода тщательно очищают от окалины, ржавчины и других загрязнений на стационарной трубоочистной машине. Очищенные трубы немедленно покрывают грунтовкой, а после ее высыхания — битумной мастикой. В условиях базы мастику на трубы наносят с помощью трубоизоляционной установки. При использовании для изоляции труб липких лент их наматывают на трубы специальными изоляционными машинами. Изоляционные работы по совмещенному методу непосредственно на трассе выполняются колонной машин, включающей краны-трубоукладчики, очистные и изоляционные машины, т.е. с совмещением процессов очистки, изоляции и укладки трубопровода в траншею.
Статья подготовлена и представлена в цифровом виде
компанией "SBH COTPAHC"
4. СПОСОБЫ УКЛАДКИ ИЗОЛИРОВАННЫХ ТРУБ И СЕКЦИЙ В ТРАНШЕЮ
Доставленные на трассу изолированные трубы или секции разгружают вдоль траншеи на расстоянии 1-1,5 м от бровки. Трубопровод в траншею можно укладывать тремя способами: 1) опуская секции или отдельные трубы со сваркой их в траншее; 2) опуская сваренные из труб или секций плети с последовательным наращиванием их в приподнятом положении или на подкладках; 3) опуская плети непрерывной ниткой с бермы траншеи.
Изолированные трубы перед укладкой в траншею укрупняют в секции с изоляцией сварных стыков. Аналогично секции укрупняют в плети или непрерывную нитку (рис. 20.7, а). Трубы или секции вначале укладывают краном-трубоукладчиком на подкладки-лежки (рис, 20.7, 6), а затем правят концы труб (рис. 20.7, в) и зачищают кромки (рис. 20.7, г).
Для центровки кромок соединяемых секций и фиксации требуемого зазора используют краны-трубоукладчики (рис. 20.7, д), внутренние и наружные центраторы (рис. 20.7, е). При сварке стыка кран-трубоукладчик поддерживает поданную секцию. Как правило, стык сваривают два сварщика (см. рис. 20.7, а), причем вначале подбирают режим и производят сварку первого (корневого) слоя (рис. 20.7, ж), а затем последующих (рис. 20.7, з, и).
Первый слой заваривают на 3/4 его длины. Затем снимают центратор и переносят его для центровки следующего стыка, куда краном-трубоукладчиком подается очередная секция. Пока сварщики доваривают оставшуюся 1/4 стыка первого слоя, монтажники готовят к сварке новый стык. Последующие слои этого стыка заваривает другое звено сварщиков, состоящее тоже из двух человек (рис. 20.7, з, и), а первые два сварщика в это время переходят к новому стыку и т.д. Неповоротные стыки сваривают снизу, лежа под трубой, уложенной на лежках (рис. 20.7, з) или в приямке траншеи. При этом режим сварочного тока подбирают с меньшими характеристиками, чем для поворотных стыков.
На практике применяют также поточно-расчлененный метод сварки неповоротных (потолочных) стыков, при котором звено слесарей-сборщиков подготавливает стык к сварке корневого слоя, а четыре сварщика быстро его заваривают. После этого они также быстро подваривают изнутри его нижнюю часть и видимые дефекты в стальной части окружности трубы. После внутренней подварки и зачистки сборщики, расчищающие наружный слой шлака, перемещаются с центратором на сборку следующего стыка, а сварщики накладывают остальные слои шва, включал облицовочный.
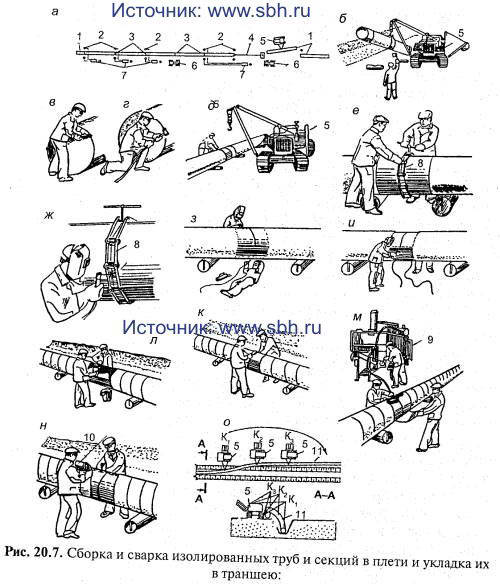
Рис. 20.7. Сборка и сварка изолированных труб и секций в плети и укладка их в траншею:
а — организация работ на трассе ; б — укладка секций на подкладки ; в , г — правка концов труб и зачистка кромок ; д — подтаскивание секций к месту монтажа стыка ; е — центрирование центратор стыка и его прихватка ; ж — подбор режима сварки первого ( корневого ) стыка ; з , и — сварка последующих слоев ; к — очистка поверхности стыка ; л , м — нанесение грунтовки и битумной мастики ; н — обертывание стыка рулонным материалом ; о— схем укладки изолированного трубопровода в траншею ; 1 — трубы ; 2 — рабочие места сварщиков и слесарей - сборщиков ; 3 — стыки свариваемых труб ; 4 — штанга с электрокабелем ; 5 — кран - трубоукладчик ; 6 — экскаватор ; 7 — электросварочные агрегаты ; 8 — центратор ; 9 — битумрплавильный котел ; 10 — оберточный материал ; 11 — сваренный трубопровод ; К1, К2, К3 — краны - трубоукладчики |
Сварку производят снизу вверх, лучше всего на токе обратной полярности, дающим большую глубину проплавления. Для более качественной сварки корневого слоя применяют газозащитные электроды ВСЦ-4, а для сварки последующих слоев - фтористокальцевые электроды УОНИ 113/55 или «Гарант», дающие хорошую пластичность и ударную вязкость сварного соединения.
При гюточно-расчлененном методе сварки труб и секций с участием нескольких сварщиков в полевых условиях необходимо для ручной дуговой сварки использовать многопостовые сварочные агрегаты постоянного тока с двигателем внутреннего сгорания (АСДП-5002, СДУ-2 и др.).
Стыки сваренных труб или секций необходимо изолировать. Для этого вначале поверхность трубы на расстоянии 0,5 м по обе стороны от стыка очищают (см. рис. 20.7, к), а затем последовательно наносят грунтовку, мастику и рулонный оберточный материал. Грунтовку наносят на сухую поверхность сразу после очистки стыка (см. рис. 20.7, л), а мастику - в горячем виде (170 — 180°С), поливая поверхность стыка из шланга от насоса котла и растирая снизу полотенцем (см. рис. 20.7, м).
Рулонным материалом стыки обертывают по горячему битуму с нахлесткой оитков 2-3 см (рис, 20.7, н). Очистку, грунтовку и изоляцию зон сварных стыков трубопроводов больших диаметров (1020- 1420 мм) можно производить механизированно, применяя комплекс типа ИС, состоящий из очистной, грунтовочной и изоляционной установок, каждая из которых поддерживается и перемещается от стыка к стыку трубоукладчиком.
Отдельные трубы и секции трубопровода укладывают в траншею стреловым краном или краном-трубоукладчиком. Длинные секции или трубы опускают несколькими кранами с помощью гибких полотенец. Для изоляции стыков трубопровода в траншее используют те же приямки, что и при сварке стыков, а горячую мастику подают непосредственно к ним, что в целом усложняет производство работ и замедляет темпы прокладки трубопроводов.
Поэтому при наличии на трассе достаточного количества кранов или кранов-трубоукладчиков, а также возможностей для сварки отдельных труб и секций в плети или непрерывную нить более эффективной является укладка трубопровода плетями или непрерывной ниткой, для чего их с бермы траншеи укладывают на дно четырьмя или тремя кранами-трубоукладчиками (рис. 20.7, о), из которых трубоукладчик К1, опускает плеть на дно траншеи, высвобождает мягкий захват и переходит в новое положение перед трубоукладчиком К3 . Затем трубоукладчик К2 опускает плеть и переходит в положение впереди К1 и т.д.
Процесс укладки сопровождается остановками, вызванными необходимостью перехода последнего трубоукладчика в голову колонны. При укладке трубопровода во избежание резких его перегибов в вертикальной и горизонтальной плоскостях краны-трубоукладчики расставляют на определенных расстояниях друг от друга в зависимости от диаметра укладываемых труб. Так, при диаметре труб до 529 мм это расстояние составляет 15-25 м; при диаметре 529 мм - 30 м; 720 мм - 35 м; 1020 мм - 30-40 м; 1220, 1420 мм - 30-40 м.
Во избежание повреждения изоляции захвата трубопровода, его подъем, перемещение и опускание следует производить при помощи мягких полотенец.
5. КОМПЛЕКСНО - МЕХАНИЗИРОВАННАЯ ПРОКЛАДКА СТАЛЬНЫХ ТРУБОПРОВОДОВ
Строительство стальных трубопроводов, как правило, ведут поточным методом, предусматривающим расчленение основных технологических процессов на отдельные комплексы и операции и последовательное их выполнение специализированными подразделениями. Основным из них является передвижная механизированная колонна (например, изоляционно-укладочная), которую с технологической точки зрения можно рассматривать как комплексную, способную выполнять основные работы поточным методом.
Способы изоляционно-укладочных работ и применяемые механизмы. Изоляционно-укладочные работы на трассе выполняются двумя основными способами - раздельным и совмещенным. При раздельном способе трубы или их секции вначале изолируют на стационарной базе, а затем сваривают на трассе в плети или непрерывную нитку с изоляцией стыков и последующей укладкой трубопровода в траншею. При совмещенном методе сваренный в непрерывную нитку трубопровод укладывает колонна передвигающихся вдоль траншеи машин, осуществляющих одновременную его очистку и изоляцию в полевых условиях.
Технологическая последовательность операций при раздельном методе такова: трубопровод сваривают в непрерывную нитку на берме траншеи из изолированных на базе секций труб и затем изолируют на трассе стыки между секциями; отрывают траншею, укладывают трубопровод с бермы траншеи на ее дно с помощью трубоукладчиков и мягких захватов (полотенец), так как применение троллейных подвесок может повредить изоляционное покрытие труб. Укладку трубопровода ведут способом последовательного переезда трубоукладчиков (рис. 20.8, а).
Однако магистральные трубопроводы чаше всего укладывают совмещенным методом, при котором все работы по очистке, изоляции и укладке трубопровода выполняет одна комплексно-механизированная изоляционно-укладочная колонна, имеющая в своем распоряжении всю необходимую технику (рис. 20.8, б).
Изоляционно-укладочные работы совмещенным методом производят с применением кранов-трубоукладчиков, которые с помощью подвижных троллейных подвесок удерживают трубопровод на нужной высоте и перемещаются вдоль трассы, сопровождая самоходные машины (см. рис. 20.8, б). Обычно в комплект машин для выполнения изоляционно-укладочных работ кроме трубоукладчиков входят очистные и изоляционные машины, установки для сушки трубопровода, битумозаправщики и др.
При совмещенном методе укладки магистральных трубопроводов к началу изоляционно-укладочных работ трубопровод на берме траншеи должен быть сварен в непрерывную нитку. Далее на трубопроводе монтируют очистную (ОМ) и изоляционную (ИМ) машины, поднимают его трубоукладчиками, расположенными на определенном расстоянии друг от друга, и начинают движение всей колонны, производя комплексно-механизированным способом очистку, изоляцию и укладку трубопровода в траншею. Источник статьи: www.sbh.ru
Для очистки трубопровода применяют самоходные одно-, двухроторные очистные машины, снабженные скребками и металлическими щетками типа ОМЛ и ОМ (см. рис. 8.1). Эти же машины наносят на очищенную поверхность грунтовочный слой, для этого их оснащают вторым рабочим органом - праймерным устройством. Для очистки и праймирования трубопроводов применяются следующие машины: для труб диаметром 168-325 мм - ОМЛ-8А; 325-529 мм - ОМ-5221; 631-820 мм - ОМЛ-4; для труб диаметром 1020, 1220 и 1420мм - соответственно ОМЛ-12, ОМ-121 и ОМ-1422.
Для изоляции очищенного трубопровода используют самоходные изоляционные машины двух типов: ИМ - для изоляции битумными покрытиями с последующей обмоткой армирующими и защитными рулонными материалами (стеклохолстом, бумагой, бризолом, гидро-изолом); ИЛ — для изоляции трубопровода полимерными лентами. Каждый тип машин выпускается нескольких типоразмеров примерно одинаковой конструкции, которые охватывают весь диапазон труб, используемых на строительстве трубопроводов. Для изоляции труб битумом применяют следующие машины: для труб диаметром 168-299 мм - ИМ-2А; 325-529 мм - ИМ-521; 631-820 мм - ИМ-17; 1020мм - ИМП-7М; 1020-1220 мм - ИМ-121 и для труб диаметром 1420 мм - ИМ-1422 (см. рис. 8.4).
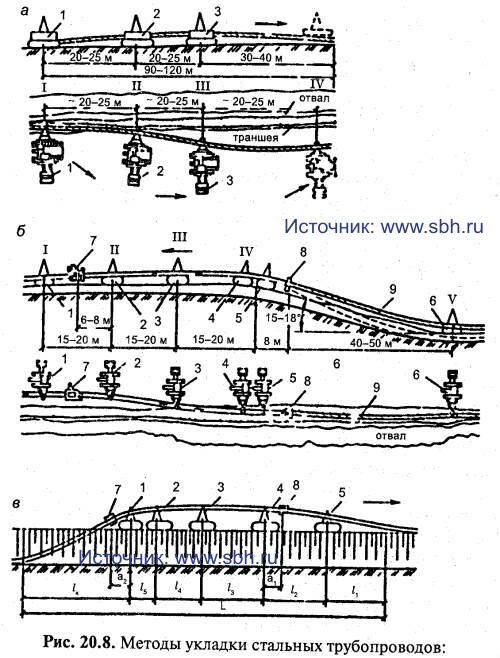
Рис. 20.8. Методы укладки стальных трубопроводов:
а и б — раздельным и совмещенным методами ; в — расстановка трубоукладчиков и других механизмов изоляционно - укладочной колонны ; 1 — 6 — краны - трубоукладчики ; 7, 8 — очистная и изоляционная машины ; 9 — изолированный трубопровод
|
В последние годы при строительстве магистральных стальных трубопроводов стали применять комбинированные машины, так называемые комбайны, выполняющие операции очистки и изоляции труб, что очень удобно при производстве работ.
Для изоляции труб липкими полимерными материалами применяют следующие машины: для труб диаметром 351-720 мм - ИМ-6П; 920-1020 мм - ИМ-19; 529-1020 мм - ИМ-25; 1020 мм - комбинированную машину ОИМ-1; для очистки и изоляции труб диаметром 1020-1420 мм - ИЛ-1422. Они движутся по трубопроводу в процессе намотки ленты со скоростью 100-300 м/ч. Машины типа ИЛ для изоляции полимерными лентами и ИМ-1422 имеют по четыре шпули, что позволяет наносить двухслойную изоляцию (см. рис. 8.4).
Технология комплексно-механизированной прокладки трубопроводов колонной машин. Для обеспечения нормальной работы очистной и изоляционной машин в процессе укладки трубопровода его поддерживают трубоукладчиками. Обычно используют пять-шесть трубоукладчиков, а для труб особо больших диаметров (1220-1420 мм) шесть-восемь и даже десять трубоукладчиков.
Характерная схема организации работы изоляционно-укладочной колонны при укладке магистрального стального трубопровода совмещенным метолом работ показана на рис. 20.8, 6. Трубоукладчики 1 и 2 с помощью троллейных подвесок поднимают трубопровод с бермы траншеи для прохождения очистной машины 7, расположенной между ними. Применение троллейных подвесок позволяет трубоукладчикам в-процессе изоляционно-укладочных работ непрерывно перемешаться вдоль траншеи с постоянным подъемом трубопровода.
По мере движения трубоукладчики 1 и 2, имея различные вылеты стрелы, смещают трубопровод в сторону траншеи. Трубоукладчики 3 и 4 поддерживают трубопровод для обеспечения возможности работы изоляционной машины 8, расположенной в конце колонны. Этими же трубоукладчиками смещают опускаемый вниз трубопровод (показан пунктиром) вместе с изоляционной машиной на ось траншеи и, таким образом, изоляцию трубопровода производят непосредственно над траншеей.
Главной особенностью совмещенного метода выполнения изоляционно-укладочных работ механизированной колонной является необходимость непрерывного удержания приподнятого участка трубопровода группой трубоукладчиков (см. рис. 20.8, 6) как при перемещении вдоль трассы, так и при многочисленных технологических остановках в течение смены.
Необходимые расстояния L между трубоукладчиками в зависимости от диаметров трубопровода при совмещенном методе изоляционно-укладочных работ, а также расстояния от очистной и изоляционной машин до трубоукладчиков приведены в табл. 20.2, составленной применительно к общей схеме расстановки машин при укладке стальных магистральных водоводов, рассмотренных на рис. 20.8, в.
Таблица 20.2 Необходимые расстояния между трубоукладчиками, очистной и изоляционной машинами в зависимости от диаметра прокладываемого трубопровода (рис. 20.8, в)
Диаметр трубопровода, мм |
Необходимые расстояния, м |
рабочие |
контрольные |
l2 |
l3 |
l4 |
l5 |
a1 |
a2 |
l1 |
lK |
L |
529 |
25 |
30 |
- |
- |
10 |
5 |
30 |
45 |
130 |
720 |
30 |
20 |
25 |
- |
19 |
5 |
40 |
65 |
175 |
820 |
30 |
20 |
25 |
- |
10 |
5 |
45 |
80 |
185 |
1020 |
35 |
30 |
30 |
- |
10 |
5 |
50 |
95 |
225 |
1220 |
30 |
30 |
30 |
5 |
10 |
5 |
55 |
100 |
225 |
1420 |
35 |
30 |
30 |
5 |
10 |
5 |
65 |
100 |
265 |
Количество кранов-трубоукладчиков в изоляционно-укладочной колонне зависит от способа прокладки трубопровода и его диаметра. На рис. 20.9 представлены рекомендуемые схемы расположения кранов-трубоукладчиков и сопутствующих машин в колонне для различных диаметров трубопроводов при их прокладке совмещенным методом, а на рис. 20.10 - то же при использовании комбайнов для очистки и изоляции трубопровода. Примерные расстояния между кранами-трубоукладчиками или их группами при этом даны в табл. 20.3.
При раздельном методе прокладки трубопровода рекомендуются другие схемы (рис. 20.1 1), а расстояния между кранами-трубоукладчиками при этом даны в табл. 20.4.
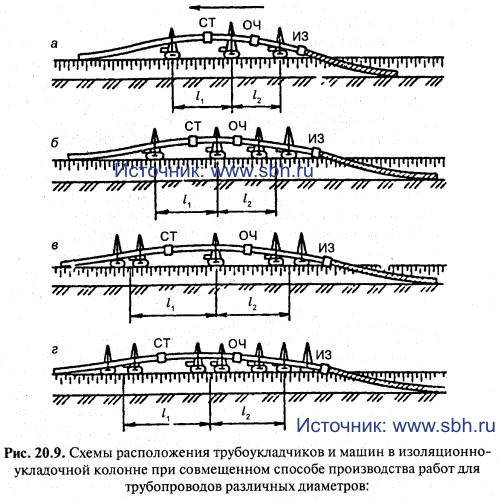
Рис. 20.9. Схемы расположения трубоукладчиков и машин в изоляционно-укладочной колонне при совмещенном способе производства работ для трубопроводов различных диаметров:
а — 529-820 мм ; 6 — 1020 мм ; в— 1220 мм ; г— 1420 мм ; ОЧ — очистная машина ; ИЗ — изоляционная машина ; СТ — сушильная установка ; l1, l2 — расстояние между трубоукладчиками и группами трубоукладчиков |
Статья подготовлена и представлена в цифровом виде
компанией "SBH COTPAHC"
Как видно из этих схем, при раздельном методе прокладки трубопровода требуется меньшее количество кранов-трубоукладчиков. Например, если при совмещенном методе для прокладки трубопровода диаметром 1420 мм требуется 7 кранов-трубоукладчиков, то при раздельном методе - всего 4. Это обстоятельство в частности и вынуждает выбирать раздельный метод прокладки трубопроводов при нехватке кранов-трубопроводов, хотя он замедляет прокладку и увеличивает ее трудоемкость.
Представляет также интерес так называемый «бесподъемный» способ укладки изолированного трубопровода на дно траншеи, образующегося как при раздельном способе прокладки стальных трубопроводов, так и при сварке трубопровода на трассе из труб с заводской изоляцией. Источник статьи: www.sbh.ru
Новый бесподъемный способ прокладки таких трубопроводов, предложенный группой специалистов Ростовского инженерно-строительного института м проектно-конструкторского и технологического института «Южтрубопроводстройпроект» (В.А. Дзюба, В.А. Облоухов, В. И Бармин, Т.М. Ядлось, Б.Ф. Белецкий и др., авт. свид. № 1682705 А1), обеспечивает укладку изолированного трубопровода на дно траншеи без традиционного его подъема кранами-трубоукладчиками с помощью мягких полотенец.
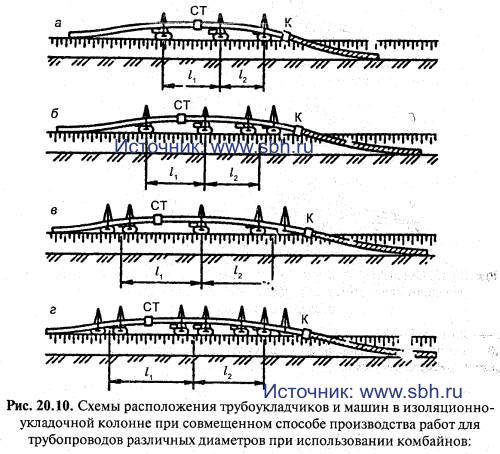
Рис. 20.10. Схемы расположения трубоукладчиков и машин в изоляционно-укладочной колонне при совмещенном способе производства работ для трубопроводов различных диаметров при использовании комбайнов;
а — 529-820 мм ; б — 1020 мм ; в — 1220 мм ; в — 1420 мм ; СТ — сушильная установка ; К — комбайн для очистки и изоляции трубопровода ; l1, l2 — расстояние между трубоукладчиками и группами трубоукладчиков
|
Таблица 20.3 Расстояния между трубоукладчиками или группами трубоукладчиков при совмещенном методе работы
Диаметр трубопровода, мм |
Расстояние между трубоукладчиками (группами), м |
Максимально допустимое расстояние между очистной и изоляционной машинами, м |
l1 |
l2 |
529 |
15-20 |
10-15 |
35 |
720-820 |
20-25 |
15-20 |
45 |
1020 |
20-25 |
15-25 |
50 |
1220 |
25-35 |
20-30 |
65 |
1420 |
35-50 |
30-45 |
100 |
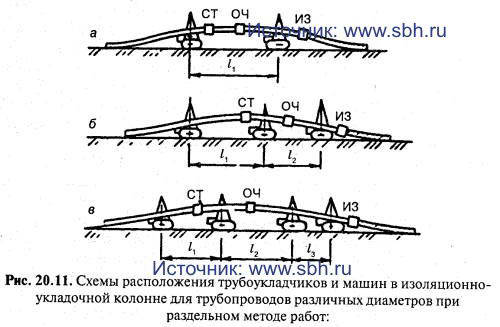
Рис. 20.11. Схемы расположения трубоукладчиков и машин в изоляционноукладочной колонне для трубопроводов различных диаметров при раздельном методе работ:
а — 529 мм ; б — 720-1020 мм ; в — 1220-1420 мм ; ОЧ — очистная машина ; ИЗ — изоляционная машина ; СТ — сушильная установка ; l1, l2, l3 — расстояние между трубоукладчиками |
Таблица 20.4 расстояния между трубоукладчиками при раздельном методе работ
Диаметр трубопровода, мм |
Расстояние между трубоукладчиками (группами), м |
Максимально допустимое расстояние между очистной и изоляционной машинами, м |
l1 |
l2 |
l3 |
529 |
15-20 |
-- |
-- |
20 |
720-820 |
15-20 |
10-15 |
-- |
35 |
1020 |
15-20 |
10-15 |
-- |
40 |
1220 |
10-15 |
15-25 |
10-15 |
40 |
1420 |
10-20 |
20-30 |
10-15 |
45 |
При этом способе траншея со стороны трубопровода, лежащего вдоль нее на берме, может быть выполнена с откосом 35-45° для предотвращения обрушения стенки траншеи, особенно если она проложена в малоустойчивых грунтах. Далее с помощью бульдозера, отвал которого облицован амортизирующим материалом, чтобы не повредить изоляцию трубопровода, начинают последовательно сдвигать его конец на ось траншеи.
Первую сдвижку трубопровода производят усилием бульдозера на расстоянии 33-46 м от начала нитки трубопровода, вследствие чего конец трубопровода зависает в траншее и фиксируется между ее стенками. Вторую сдвижку трубопровода делают на расстоянии 46-58 м от начала нитки, вследствие чего конец трубопровода длиной 200 — 250 м и массой до 120 т (при диаметре 1420 мм) зависает в траншее, изгибаясь под собственным весом в вертикальной плоскости. В то же время трубопровод под воздействием внешней сдвигающей силы от бульдозера изогнут в горизонтальной плоскости, т.е. имеет место сложный пространственный изгиб при известной жесткости трубопровода, когда в нем возникают упругие напряжения.
Стальной трубопровод как упругая система, подвергающийся воздействию внешних сил, имеет потенциальную энергию деформации упругого изгиба, В то же время упругая система стремится к своему равновесному состоянию, которым для трубопровода является его стремление к восстановлению своего прямолинейного положения. Поэтому трубопровод, находясь в напряженном состоянии, начинает самопроизвольно укладываться в траншею за счет потенциальной энергии изгиба, переходящей в кинетическую. При этом трубопровод восстанавливает свое устойчивое положение, а внутренние напряжения снимаются. Процесс укладки трубопровода на дно траншеи происходит быстро без его перекатывания и закручивания.
Предложенный способ имеет ряд преимуществ, так, он не требует подъема, перемещения и опускания трубопровода в траншею, для чего требуется 5—6 кранов-трубоукладчиков, а все это заменяется сдвижкой его конца в траншею бульдозером. Поскольку при этом способе не требуются краны-трубоукладчики для подъема трубопровода, то способ можно назвать и бескрановым.
В зимний период изоляционные работы осложняются отрицательным влиянием низких температур на применяемые изоляционные материалы. Поэтому изоляционное покрытие на трубопроводы допускается наносить при температуре не ниже -35°С. В зимних условиях в районах крайнего Севера в состав колонны включают трубо-нагревательную печь СТ, которую ставят перед очистной машиной.
Особенности изоляции трубопроводов полимерными лентами. Перед началом работ изоляционная машина должна быть заземлена, а также оборудована устройством для снятия статического электричества с поверхности ленты. Изоляционные ленты следует наматывать на трубопровод по свеженанесенной (невысохшей) грунтовке при температуре окружающего воздуха не ниже -40°С. При температуре воздуха ниже +10°С рулоны ленты и обертки перед нанесением необходимо выдержать не менее 48 ч в теплом помещении при температуре не ниже +15°С (но не выше +45°С). При температуре воздуха ниже +3°С поверхность изолируемого трубопровода надо подогревать до температуры не ниже +15°С (но не выше +50°С).
Изоляционные и оберточные ленты наносят без перекосов, мор- л щин, гофр, отвисаний с величиной нахлеста: для однослойного покрытия - не менее 3 см, для двухслойного - на 50 % ширины ленты плюс 3 см.
Угол наклона шпуль регулируют, усилие натяжения измеряют динамометром. При установке на шпулю машины нового рулона ленты конец нанесенного полотнища нужно приподнять на 10-15 см и под него подложить начало разматываемого рулона. Эти концы разглаживают на изолируемой поверхности и затем прижимают рукой до нахлеста их последующим витком ленты. При изоляции трубопроводов импортными лентами у сварных швов допускается, как исключение наличие узкой (1,0-1,5 мм) полосы с неплотным прилеганием изоляционной ленты; эти неплотности при засыпке трубопровода должны исчезнуть.
Изоляционную машину перед нанесением лент необходимо тщательно отрегулировать по диаметру изолируемого трубопровода и ширине нахлеста. Постоянно следует также проверять натяжение ленты и состояние ходовых колес; при необходимости следует производить их регулировку.
Трубы из углеродистой стали подвержены интенсивной коррозии, которая составляет в системах водоснабжения 0,05—0,8 мм/год. Этого можно избежать, используя стальные цементно-полимерные и цементно-песчаные покрытия внутри труб.
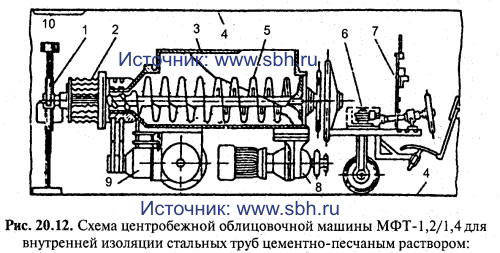
Рис. 20.12. Схема центробежной облицовочной машины МФТ-1,2/1,4 для внутренней изоляции стальных труб цементно-песчаным раствором:
1 — заглаживающая лопатка ; 2 — разбрыгзгивающая головка ; 3 — бункер машины ; 4 — облицовываемый трубопровод ; 5 — шнек ; 6 — механизм рулевого управления ; 7 — приборный щит ; 8 — мотор - редуктор ; 9 — привод разбрызгивающей головки ; 10 — цементно - песчаная облицовка |
Академией коммунального хозяйства им. К.Д. Памфилова разработана центробежная облицовочная машина МФТ-1,2/1,4 (рис. 20.12), принцип работы которой заключается в следующем. Цементно-песчаная смесь подается в бункер, из которого при вращении шнека она поступает в центральную трубу машины. Выжимаясь через продольные щели на ее конец, бетонная смесь попадает на лопатки вращающегося метателя и под действием центробежных сил отбрасывается к стенкам облицовываемой трубы, т.е. покрытие наносится центробежным набрызгом. Нанесенный раствор одновременно разравнивается вращающимися подпружиненными лопатками. Они заглаживают и калибруют нанесенный мелкозернистый бетон, образуя равномерный слой толщиной 12 мм. В процессе работы машина движется внутри трубы со скоростью 0,3-0,5 м/мин. Источник статьи: www.sbh.ru
Результаты многолетних наблюдений за состоянием покрытий позволяют установить, что срок их эксплуатации составляет не менее 50 лет.
Статья подготовлена и представлена в цифровом виде
компанией "SBH COTPAHC"
Продолжение... Бестраншейная прокладка труб под дорогами и другими преградами.
|